Use visual controls to drive action across your visual management systems. In brief, visual controls are effective in standardising decisions across your standard operating procedures. For example, visual controls can be implemented to maintain your safety and quality standards. Read on for more examples of visual controls.
Colour coding your visual management process
Visual controls – colour coding
Above all, show a process’ status in a way that is easy to understand, at a glance. Furthermore, show status in real time. Furthermore, colour coding visual controls can aid your team to understand the next action to take.
In addition, site wide colour coding ensures a uniform response to any issues. Colour coded visual controls can be used for Shadow Boards, Floor Markings, Red Amber Green status and more.
See more on colour coded visual management boards.
Visual controls – status indicators
Firstly, Red Amber Green (RAG) is a highly effective colour coding system. Secondly, it is universal and therefore, easy to understand at a glance. Furthermore, use it to show status in real time. In other words, progress or targets right now. Most importantly, show status to instantly assess progress and prompt next actions.
In addition, use status indicator meters or sliders with colour coded magnetic status labels, such as Red/Sad and Green/Happy faces. Consequently, assess progress and tasks instantly and easily.
Read more on Visual Status Indicators.
Combine status indicators for ultimate visual controls
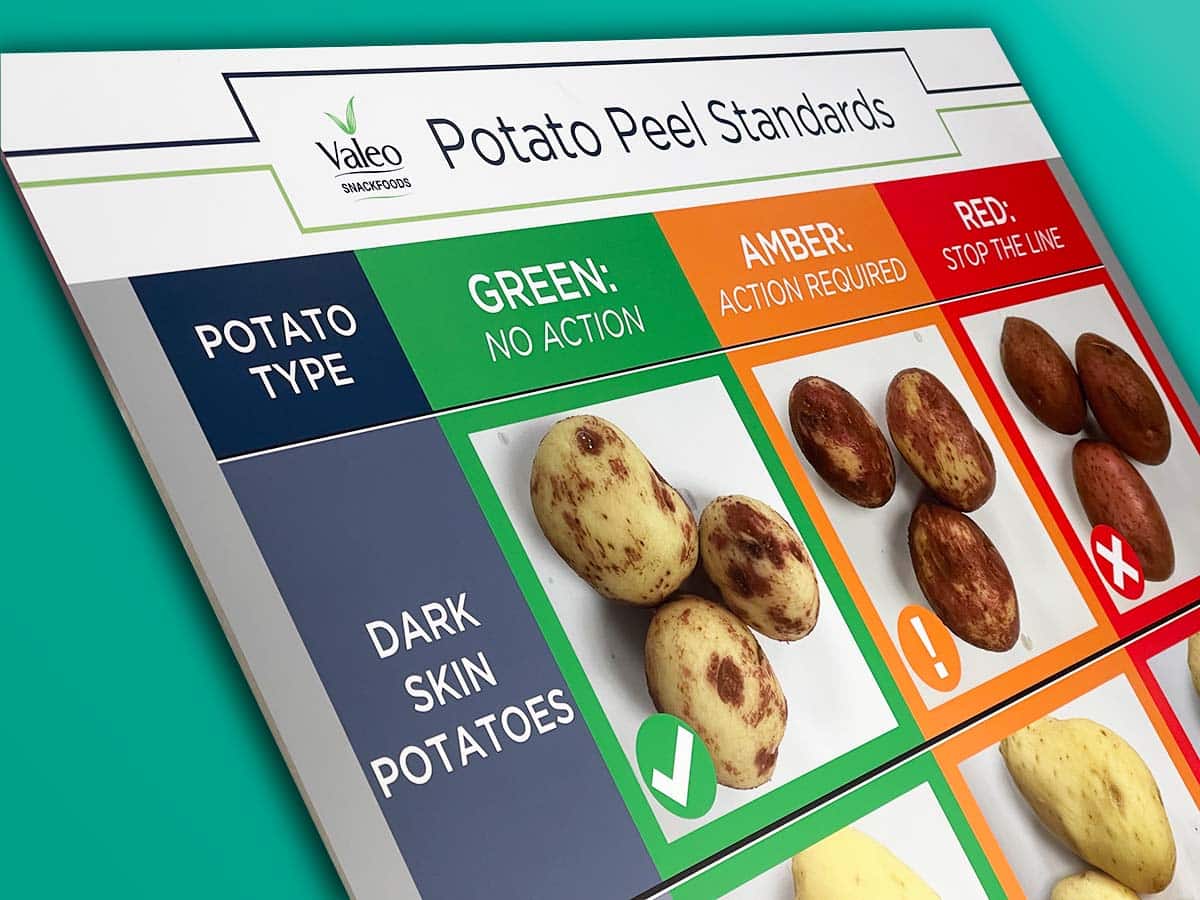
Visual controls for quality standards
Visual controls – quality standards
In short, a visual control quality standards board shows your standards in a way that’s immediately clear.
Most importantly, show what good looks like. In other words, set your standards visually. Therefore, show what good looks like using pictures. Likewise, say what good is using words. Make your own quality rules clear. Images, text and colours are used to make clear what actions to take. Improve understanding and therefore, efficiency.
Read more on Visual Standards.
Visual controls – Standard Operating Procedures
Standard Operating Procedure Boards work because they show your procedures in a visual, step-by-step way. They provide the most relevant information for the given procedure. Furthermore, they uphold your standards in a consistent way. In other words, they support uniformity in quality standards and performance. Similarly, they reduce miscommunications relating to procedures. Finally, they support the team to comply with regulations. Above all, they are an instantly accessible visual reference for all the team to work from.
Read more on Standard Operating Procedure Boards.
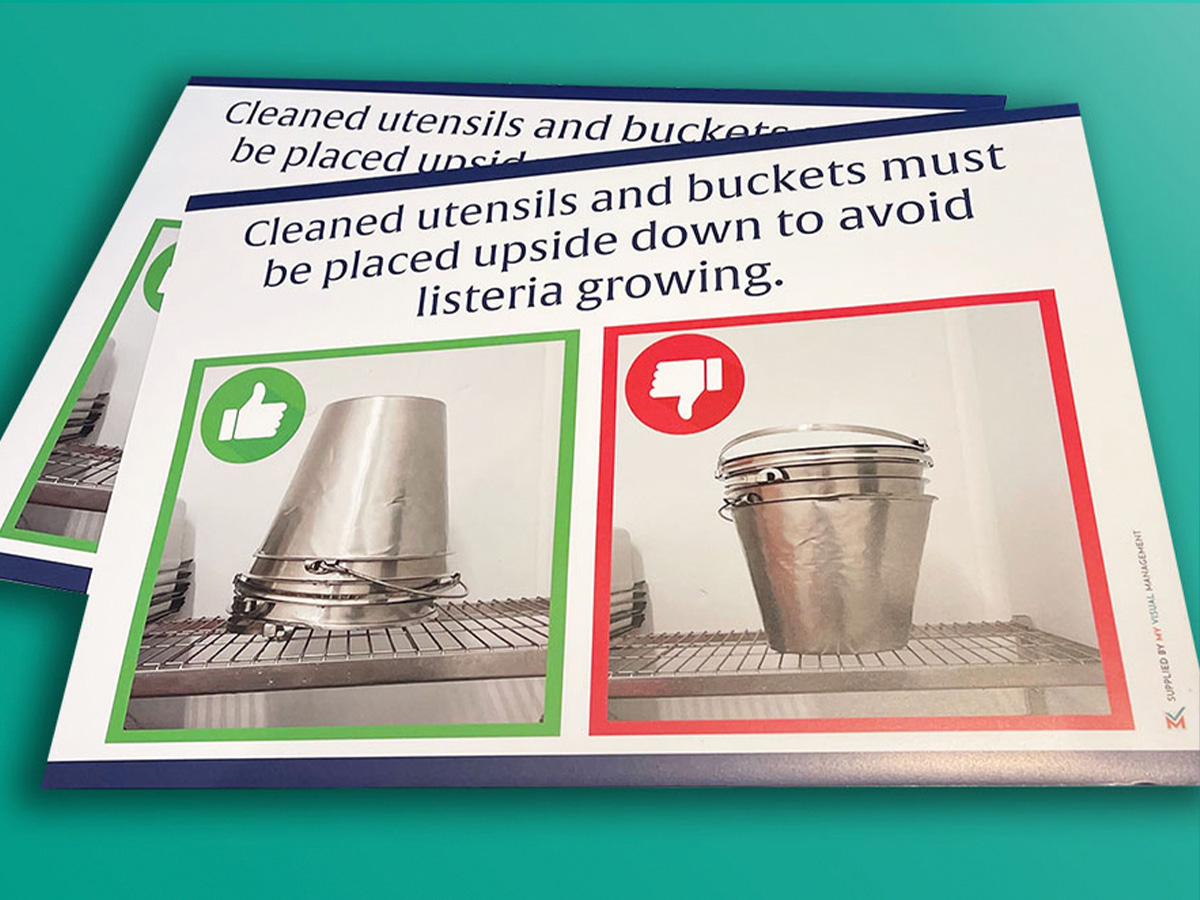
Show standard operating procedures visually
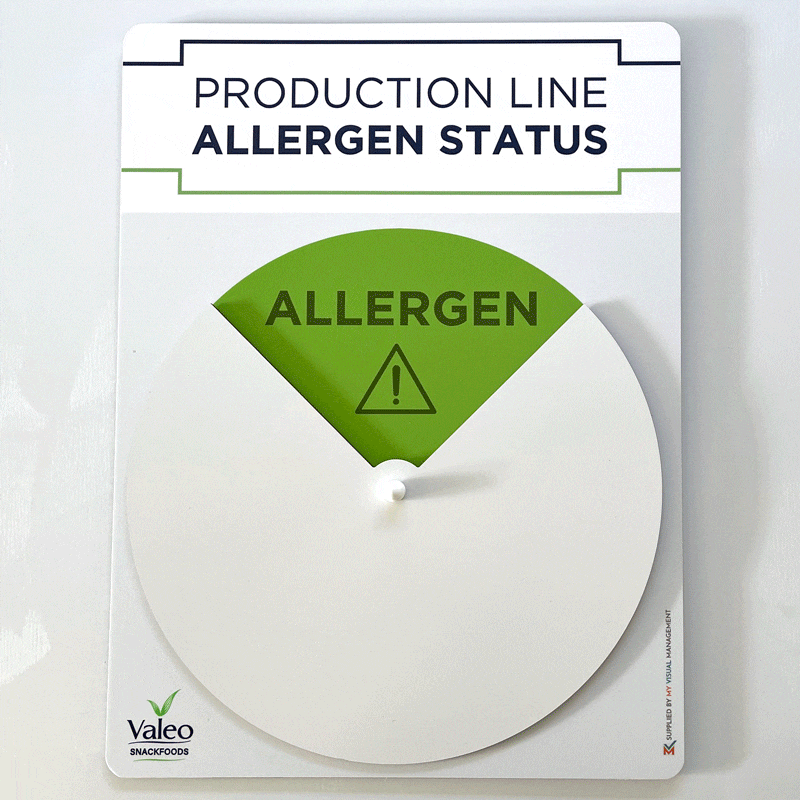
Make allergen control visual and immediate
Visual controls – allergen control
Make your own visual allergen status indicator. As a result, make allergen control visual, visible and quick to update in real time.
Firstly, this specialist visual allergen status indicator fits close to the process. For example, it fits above (or near) the production line. As a result, the line operator can immediately update allergen status. Most importantly, without having to leave the line. In other words, without the need to collect status magnets or dry wipe pen. Status is extremely visible and accessible for all to see, at a glance. Above all, it works in a way that is safe, quick and easy to use.
Read more on Allergen control.
Visual controls – Kanban boards
So, Kanban boards originated as part of the Toyota manufacturing process. They are used to display the entire work process, rather than individual tasks. Consequently, each of the cards on the Kanban board move across the colour coded columns, showing each step of the process. Furthermore, issues can be highlighted and a visual snapshot provided.
Kanban Board for optimising workflow
Engage your team
Visual controls – OPEX
Make an OPEX Board to support Operational Excellence in your workplace. In other words, make OPEX visual and accessible, on a daily basis. As a result, make it a visible part of your organisation’s strategy and culture.
Above all, drive and deliver Continuous Improvement and Kaizen with your OPEX Board. Most importantly, use your OPEX board to visually engage your team. As a result, make Operation Excellence central and habitual.
Read more about this OPEX example.
Visual controls – Shadow Boards
Custom made shadow boards and cleaning stations work because they instantly show when a tool is missing. Furthermore, they show the shape of the missing tool. Importantly, our shadow boards and cleaning stations are custom made. Firstly, to show your specific equipment or clothing. Secondly, they are sized to fit your space. Finally, choose from hooks, pegs or whatever you need to best make the board work. In short, your board is made to keep your workplace tidy and well organised.
Read more on Tool Shadow boards.
Visual control shadow board
Way finding markings provide directions around your workspace
Visual controls – floor markings
Above all, custom floor markings for visual management work by organising your workspace. For example, mark out different areas in a clear way on the floor. Likewise, segregate key areas, or equipment. Furthermore, show where machinery lives when not in use. For instance, fork lift trucks. Therefore, floor tape and labels work for ordering machinery and equipment. Finally, use custom floor markings as part of your 5S strategy.
Read more on floor markings.
Examples of our Visual Controls
You May Also Like
Our Approach
We create visual management displays and boards everyday. As a result we have plenty of experience. We work for organisations in food production, the power industry, national rail, pharmaceuticals, education, healthcare, packaging and distribution.
Our team works with a simple idea or sketch and creates a professionally designed layout. This is then turned into a highly functional and visual board.
We offer customised options because we want to create the perfect board for you. So, here are a few examples. We can add magnetic areas or a dry-wipe finish (for use with whiteboard pens). Furthermore, you can choose Red/Green sliders or R.A.G. (Red, Amber, Green) status dials so you can quickly and visually update your board. These are just a few examples of the ways in which our boards can be tailored to meet your needs. You may also be interested in whiteboard overlays that can be used on top of an existing magnetic board.