Create 5S visual management boards to organise your workspace. Work smarter (literally). Increase performance and productivity. Above all, create your own 5S visual management board to make ordering your workplace easy for all the team.
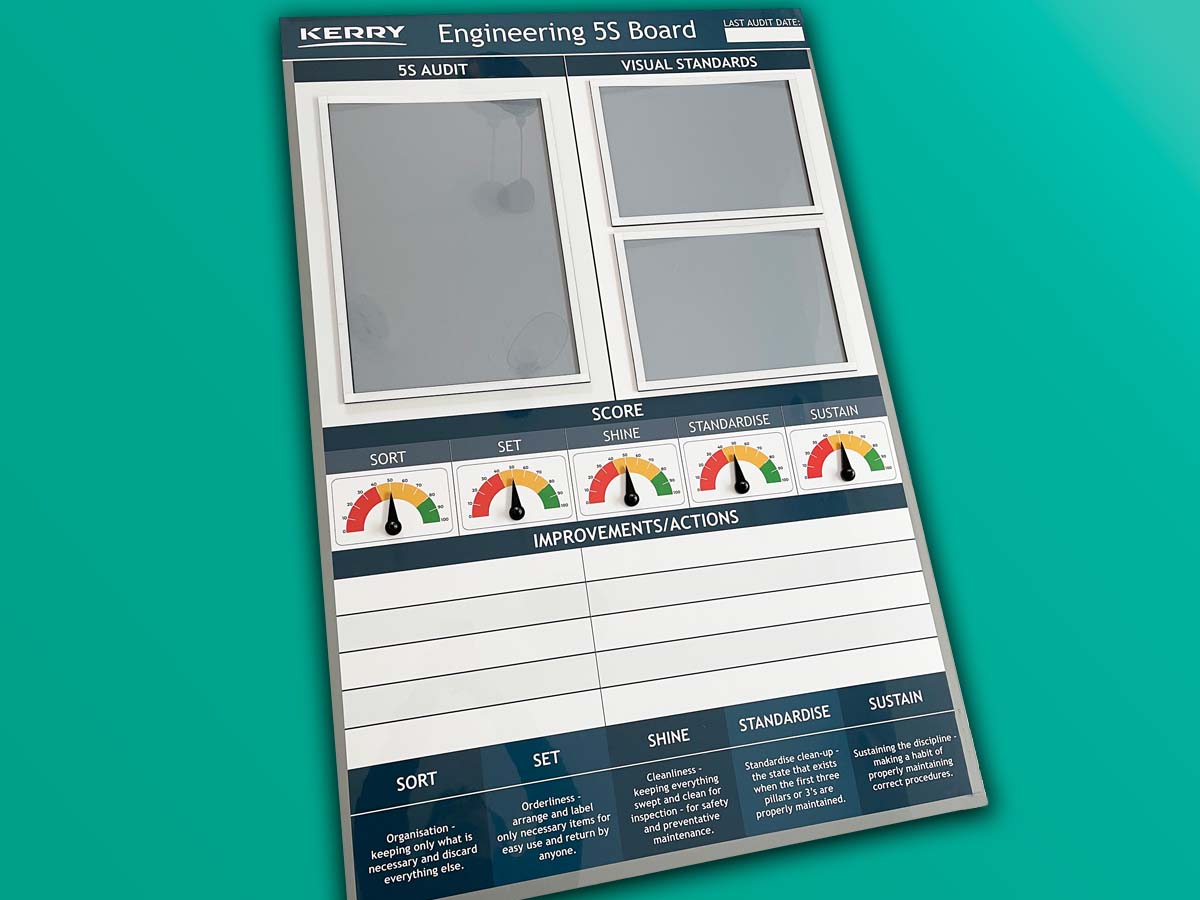
Make your board dry wipe. Likewise, add status indicators or document holders
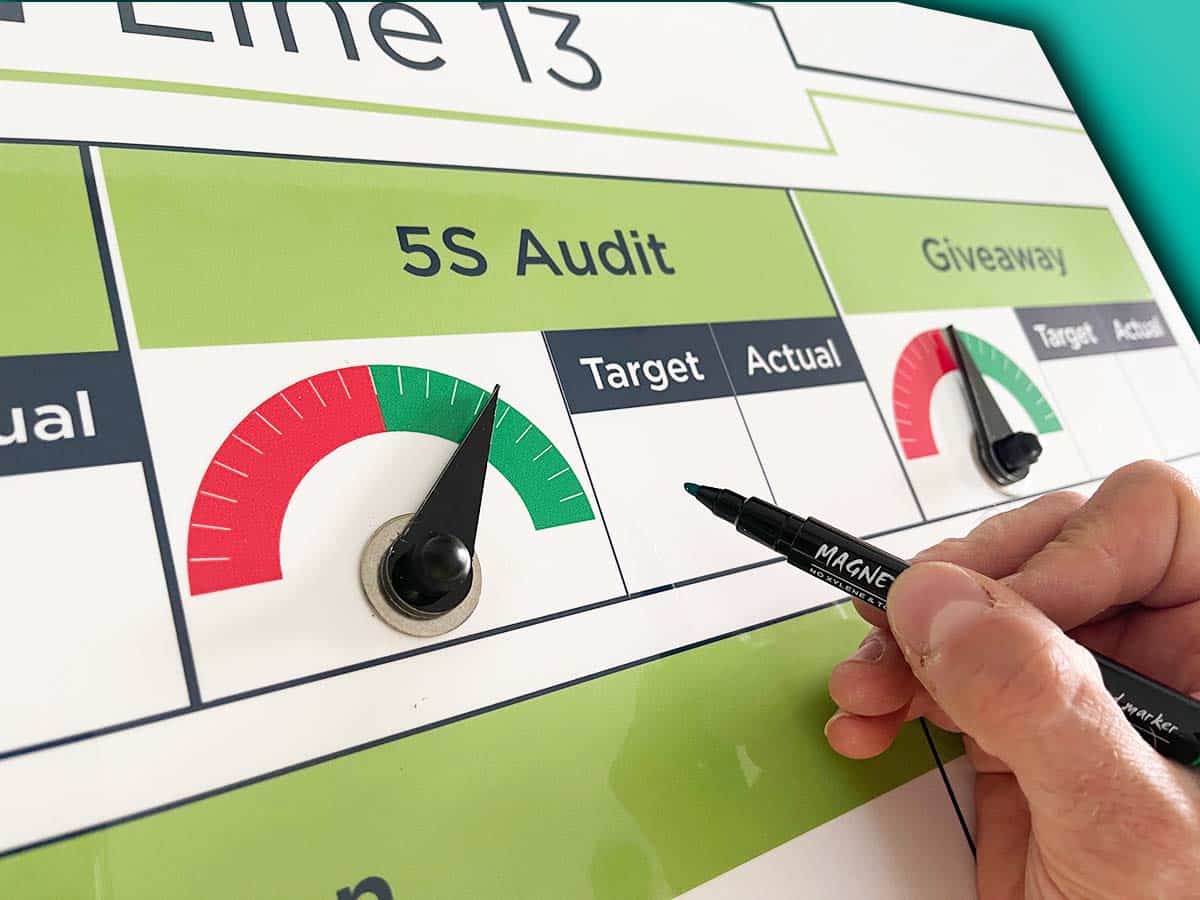
Use your 5S board to assess your daily progress
5S Overview
5S is an assessment process for organising your workplace.
Originating from Japan, this method focuses on five Japanese words. These all start with an ‘S’ hence the “5S” title. Furthermore, these translate as “Sort”, “Set in order”, “Shine”, “Standardise” and “Sustain”.
Above all, make your own 5S visual management board to show the 5S process in a visual way. Break it down into each of the five steps.
Most importantly, use your 5S board to assess you progress and track results.
5S: defining each S
Firstly, “Sort” refers to assessing all equipment and items in the workspace. In other words, it’s the decluttering phase. Above all, determine if anything needs to be removed, recycled or relocated. Furthermore, take action.
Use this section of your own 5S board to show how this process works in your workplace. Likewise, make it clear to all your team, at a glance.
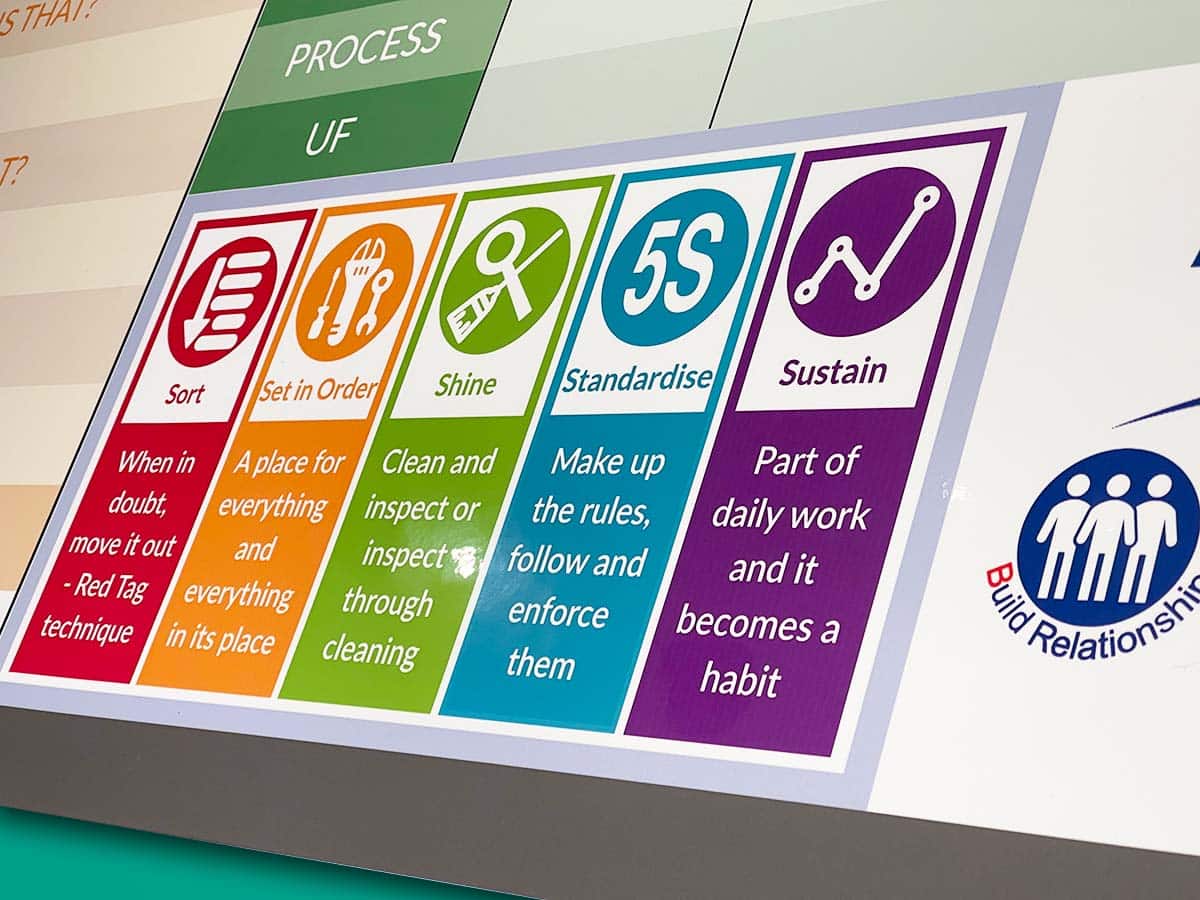
Colour coding helps focus on each 5S section
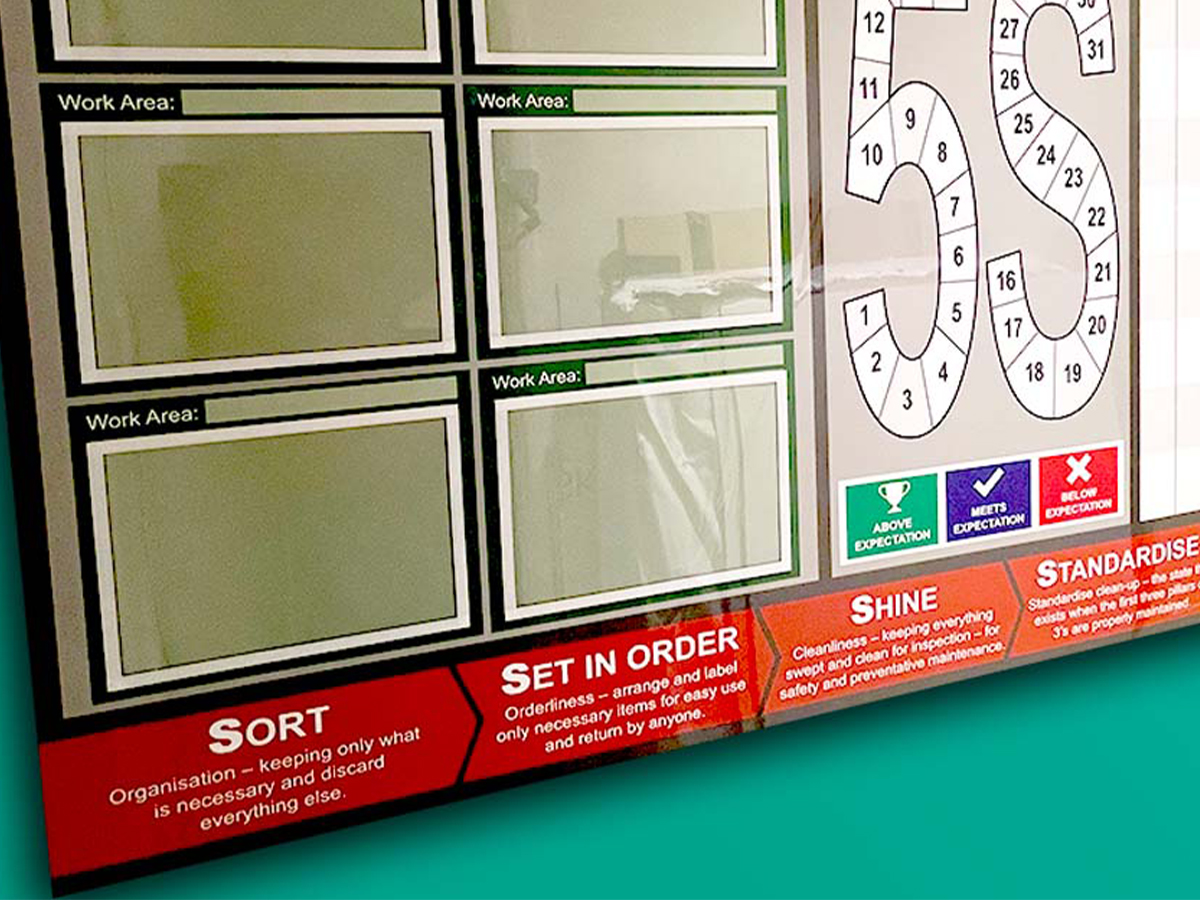
Order equipment to cause least waste of time, space and effort
Secondly, “Set in order”. That is to say, what is the most logical way of setting out and storing equipment? This requires thinking in terms of space, frequency of use and so on. Ultimately, equipment needs to be ordered in a way that causes least waste of time, space and effort. Creating your own tool shadow boards helps this part of the process.
Meanwhile, “Shine” refers to cleaning the workspace. It also extends to keeping equipment and machinery in good order. That is to say, planning, scheduling and managing regular maintenance checks. Use your 5S Visual Management Board to show this procedure in a visual way.
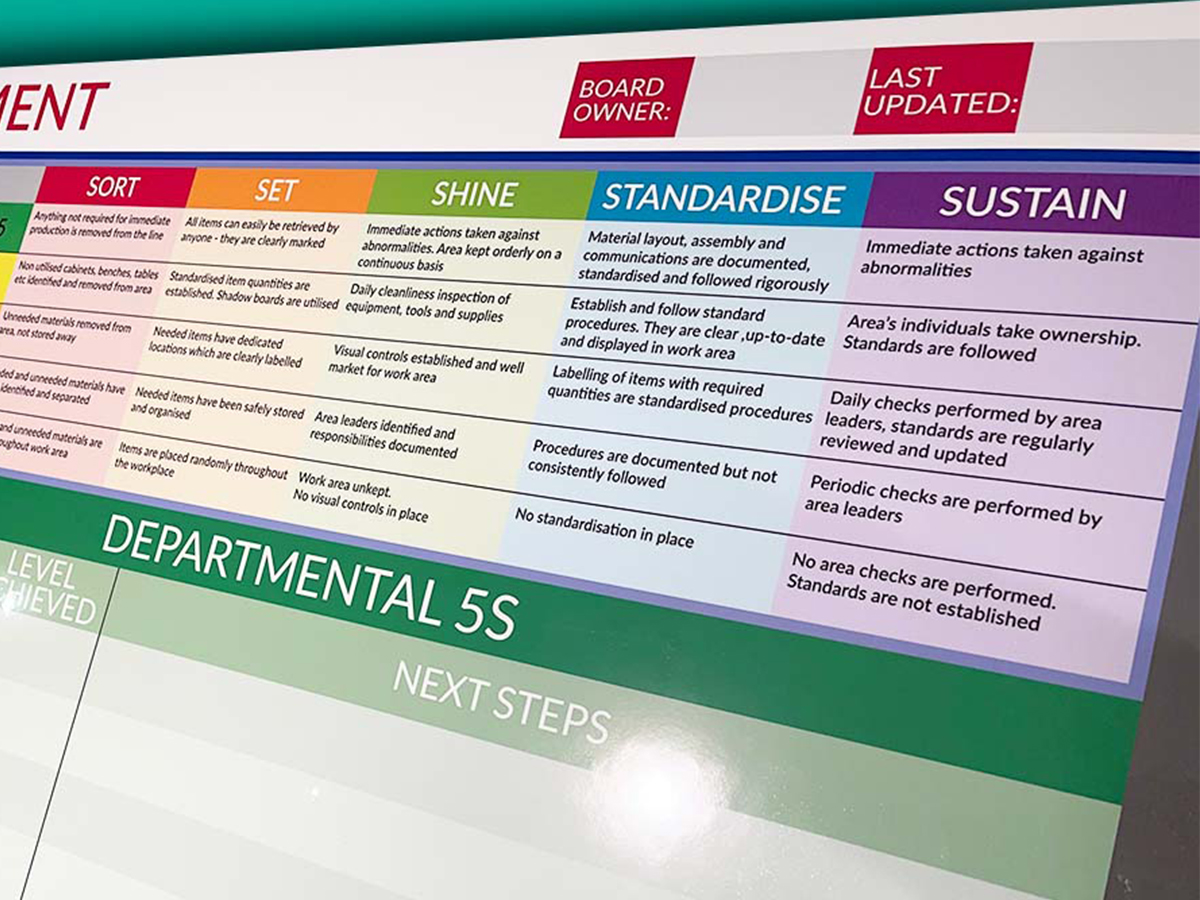
Make each stage visual
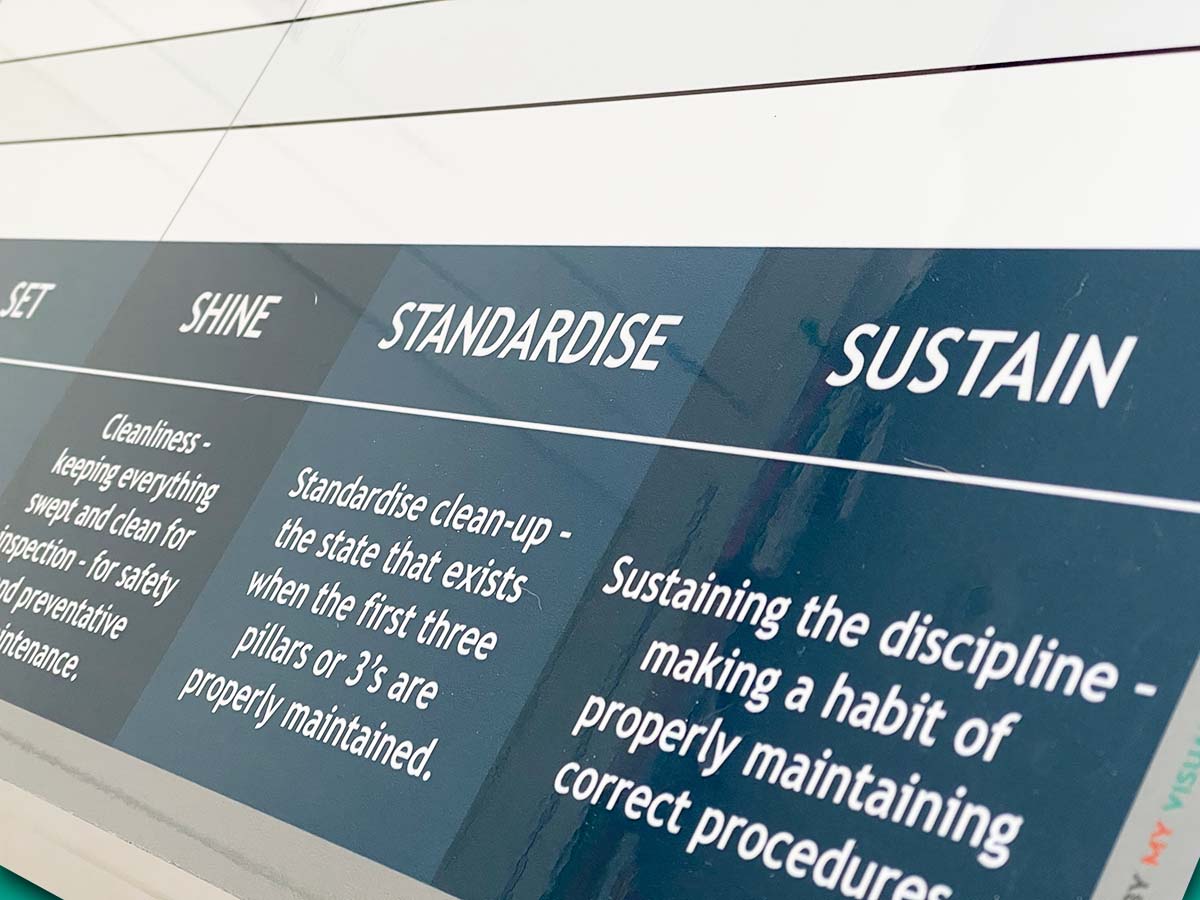
Most importantly, make 5S, or 6S, a habit
Subsequently, “Standardise” means turning the activities of the first 3 Ss into a continuing habit. In other words, create standard operating procedures to maintain an orderly and organised workspace. Most importantly, this is where visual management works. Custom make your very 5S board in support of this. Use it to set and show your 5S standards in way that is immediately clear.
5S Examples
Task list for 5S
So design your 5S board to include and record a task list. Furthermore, with red green status sliders for instant tracking. Above all, reflect your processes visually and increase engagement with your 5S or 6S strategies.
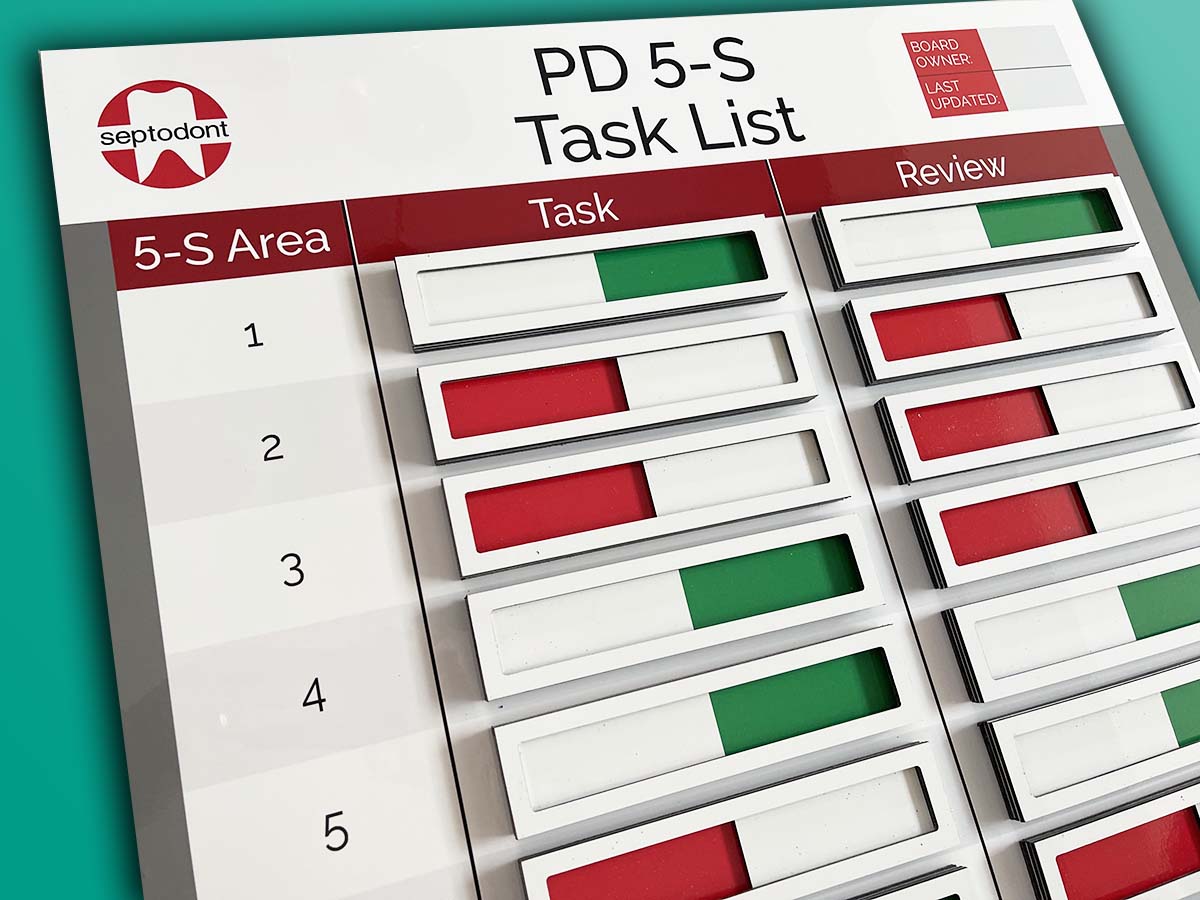
Create a 5S or 6S task list
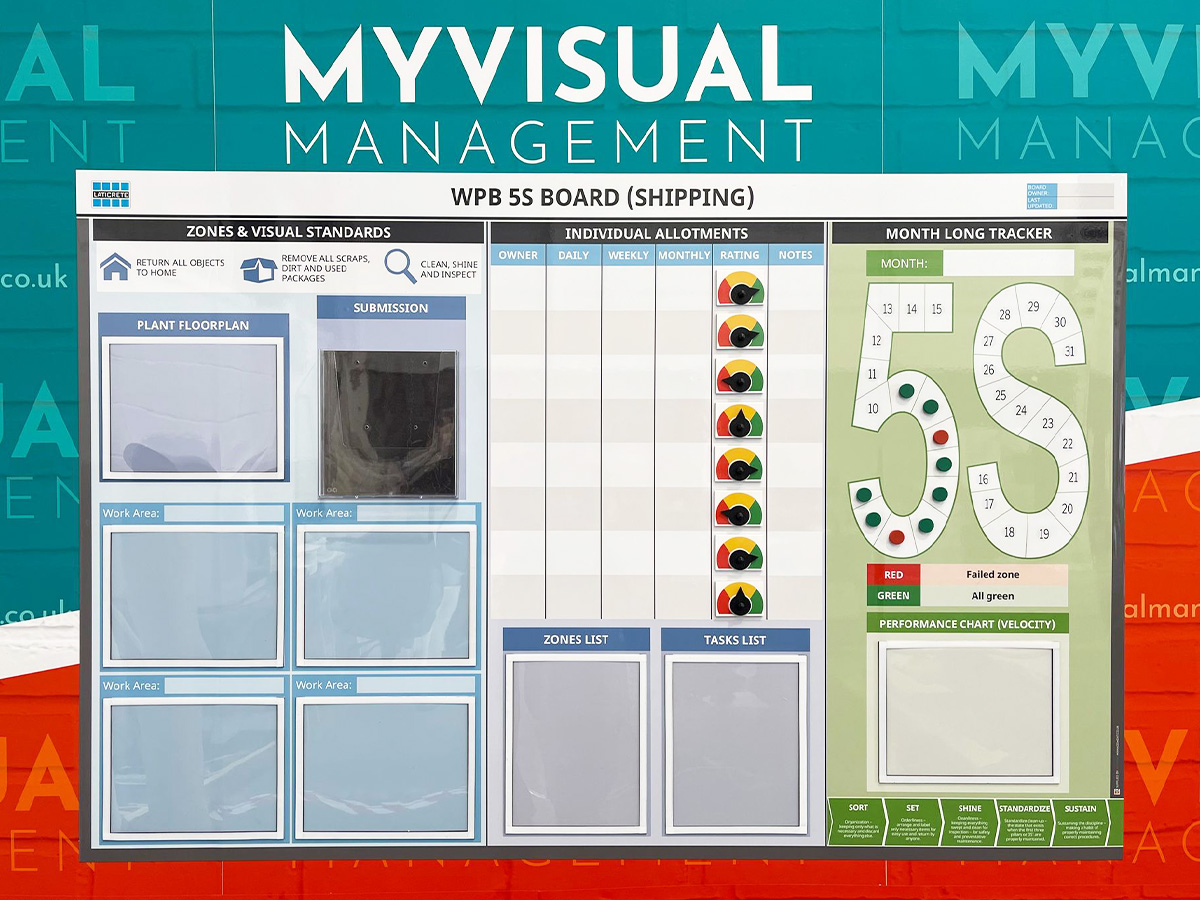
Ideal for 5S production and shipping
5S for production and shipping
These 5S type boards can include all the information you need to process your products. Display visual standards. In addition, include status indicator meters for a visual snapshot of progress.
Likewise, use magnetic status counters to track your daily 5S progress.
5S boards for shift patterns
So design your 5S board to include and record single/double or even triple shift patterns. Furthermore, with a dry wipe option for easy recording. Above all, reflect your processes visually and make easy daily updates.
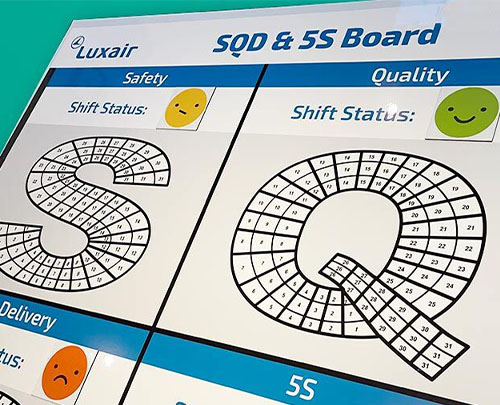
Use single, double or triple shift patterns on your SQDC board
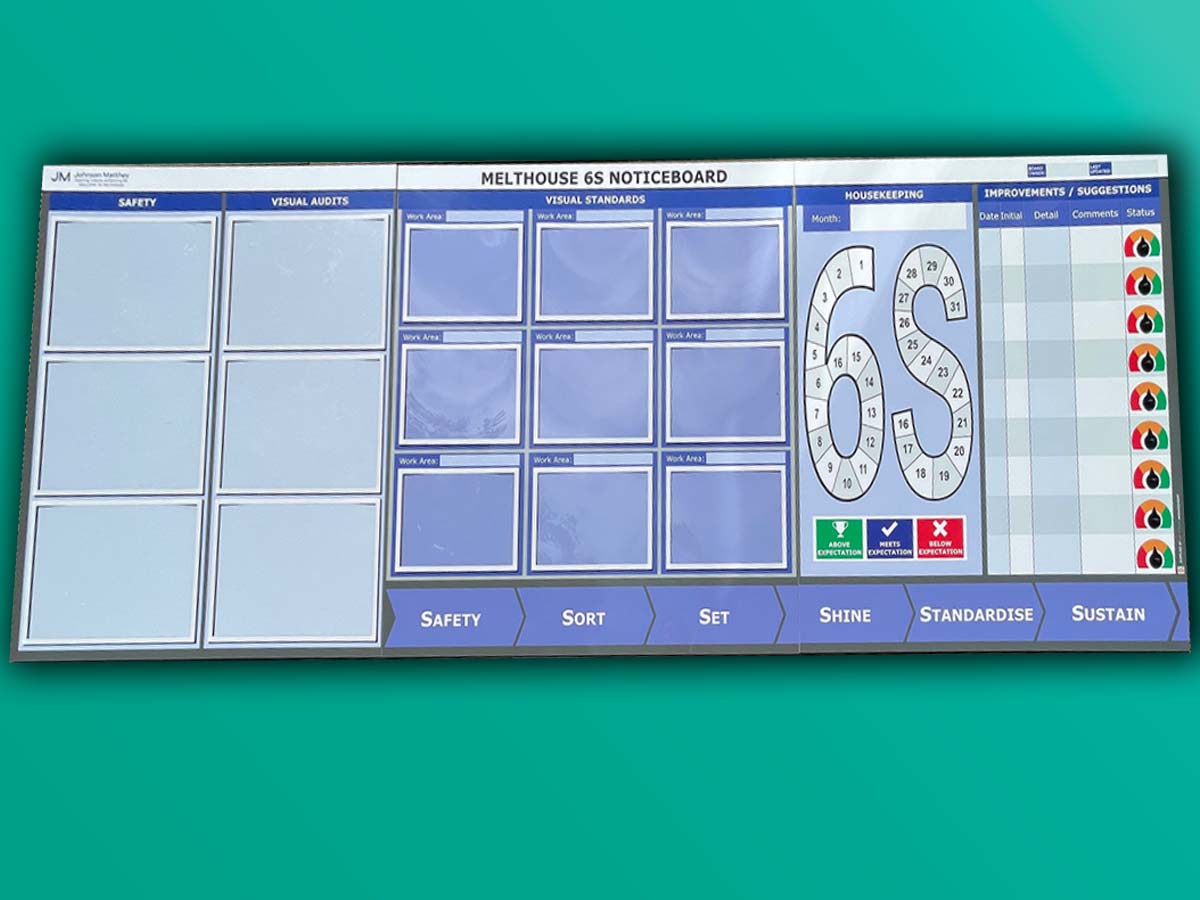
Consider 6S housekeeping option
6S visual management
Furthermore, choose to incorporate 6S into your housekeeping strategy. Therefore, Sort, Set in order, Shine, Standardise, Sustain and Safety.
In addition, use status indicators to show progress and status. For example, status indicator meters or status dials. Also, you might want to add document holders to store tickets or information relating to each 6S category. See more examples and information on 6S visual management boards.
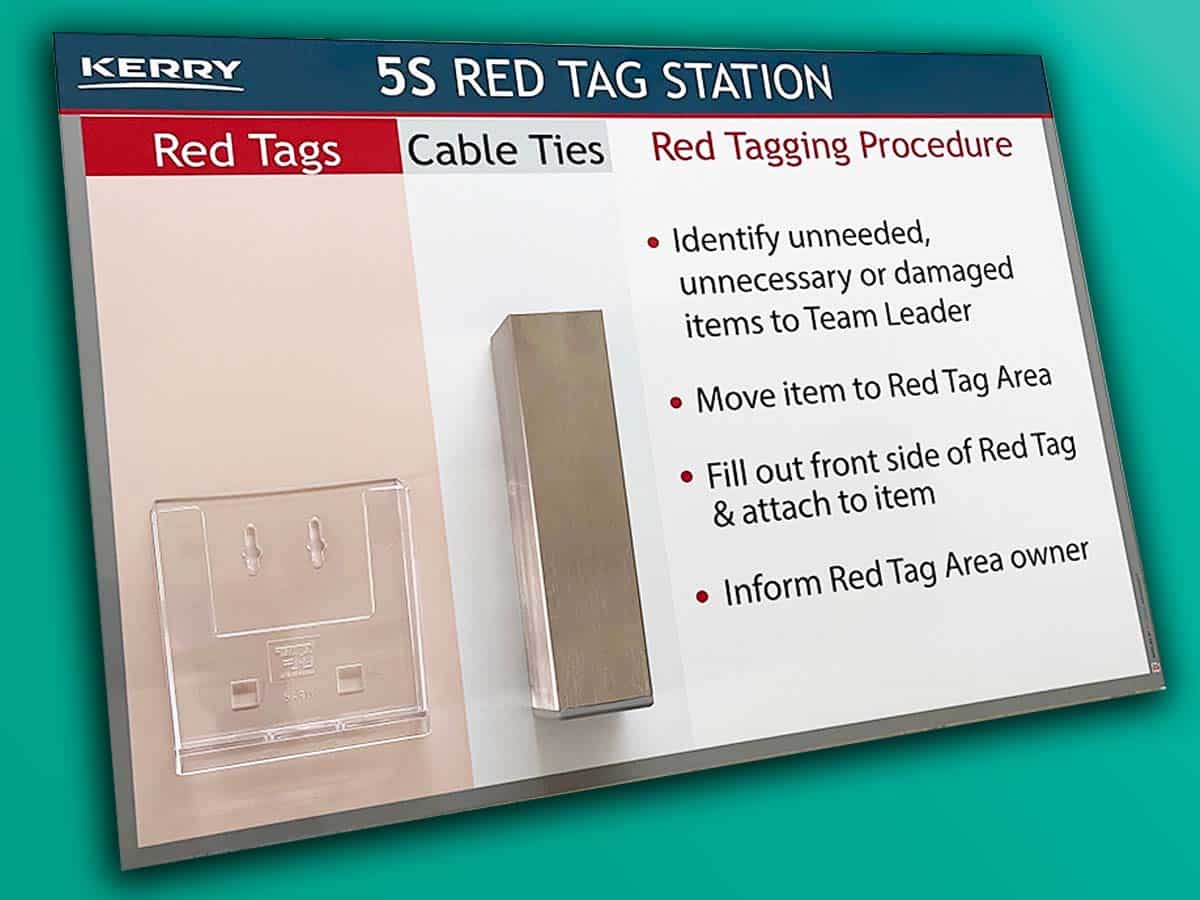
Support your 5S strategy with a Red Tag station
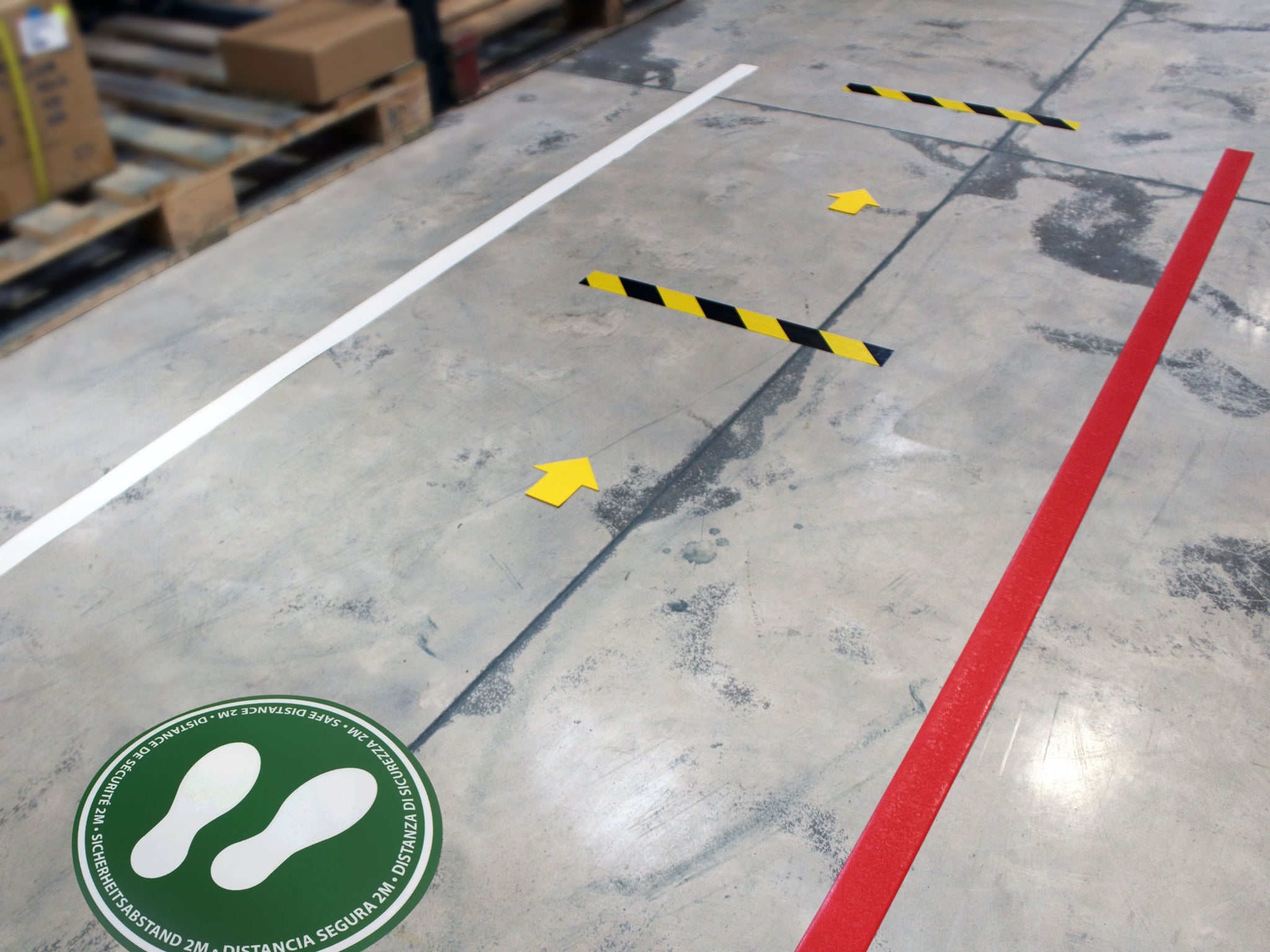
Floor markings for safety and organisation
Further Visual Management ideas for 5S
Firstly, use a 5S Red Tag station to remove unnecessary items from your workspace. In other words, eliminate any waste of space. Likewise, support a zero-waste strategy. As a result, organise your work setting better and increase efficiency. The Red Tag process enables team members to rid the workspace of unneeded items or tools. It also enables them to try living without the item before getting rid of it for good. In addition, the process encourages a regular habit of sorting, which supports 5S.
Secondly, floor markings are useful to organise your workspace. Segregate key areas, or equipment. Furthermore, use them to mark out different areas in a clear way.
Use labels and signs to show key information about equipment. For visual effect, consider colour coding.
You might want magnetic document holders or numbered magnetic stickers, so choose magnetic areas on your board. Similarly, you might want to add colour coded updates for instant visibility. These are just some examples of how our boards are further customised to meet your needs. We do this because, above all, they are made to work for you.
You May Also Like
Our Approach
Most importantly, we make visual management boards everyday. As a result, we have so much experience. Furthermore, we work for organisations throughout the UK. Likewise, in Europe and America. Similarly, we support businesses in a range of sectors. Firstly, food production. Secondly, utilities and transport. In addition, pharmaceuticals, education and healthcare. Furthermore, logistics and distribution. Above all, our team works with a simple idea or sketch you have. Subsequently, we custom make you a professional visual management display. As a result, we custom make you a highly functional visual management board. We offer options so we make the perfect board for you. So, here are a few examples. Firstly, for instance, we add magnetic areas. Similarly, a dry wipe (dry erase) finish. Furthermore, choose status indicators. in addition, board accessories. Therefore, quickly update your board. Above all, in a visual way. In short, make your processes visible. similarly, accessible. Most importantly, at a glance. These are just some examples of the ways in which we meet your needs. Read further visual management resources articles. Similarly, visual management case studies.